Surrounded by three mountains, the factory is located in Cháozhōu, a charming city situated in the eastern part of Guangdong Province, which also considers itself to be the “Ceramic Capital of China”. The ceramics factory manufactures different items from hardened clay: anything from tableware and mugs to sculptural vases and our beautiful Shell Pot. Despite the fast-changing world, the 60 employees at the factory remain loyal to the true spirit of craftsmanship at every stage of production.
The materials
The raw materials used for ferm LIVINGs ceramics are all carefully sourced and quality checked to ensure that every ferm LIVING product is of the utmost quality. The clay used has been vacuumed and de-aired to suck out any air pockets introduced by the clay-making process. Built to last a lifetime, the materials used are extremely durable.


The process
The ceramic-making process is slow and complex and is handled by several different people, each an expert in their profession. Pottery with delicate or detailed silhouettes like our Shell Pot often requires a combination of traditional and modern tools and production techniques such as slip casting, hand painting, sponging, trimming, dipping and glazing.


“The ceramic-making process is slow and complex and is handled by several different people”
The ceramic object is often formed by slip casting, where perfectly mixed clay is poured into a two-part plaster mould to harden and dry. The plaster mould expedites the drying process, as it soaks up some of the excess water from the clay. It is a skill in itself to separate the two parts of the plaster mould at the perfect time. The clay must be almost completely hardened, yet also still a bit moist for the potter to trim the item.
“ It is a skill in itself to separate the two parts of the plaster mould at the perfect time”
From this point, a potter begins trimming by hand using a hand-thrown pottery wheel, a damp sponge to clean the pot continuously and special metal tools with angled blades and wire loops to smooth the roughness and rims. It takes a lot of practice to recognise the perfect consistency for trimming pottery, and how much to take off without damaging the surface. Before being passed to a colleague, the pot is examined for its evenness and aesthetic beauty. Now the pot is ready for its first firing in a special kiln running at 800°C for 7-8 hours.
Deep hollowware such as our Shell Pot must be flushed with a reactive glaze by hand to ensure a complete coating on the inside to make the pot virtually impervious to liquid. After glazing, the pot requires a second firing for up to 12 hours, this time at 1,230°C, to achieve the right shape and longevity. Finally, every single product is carefully inspected to ensure it meets our requirements.
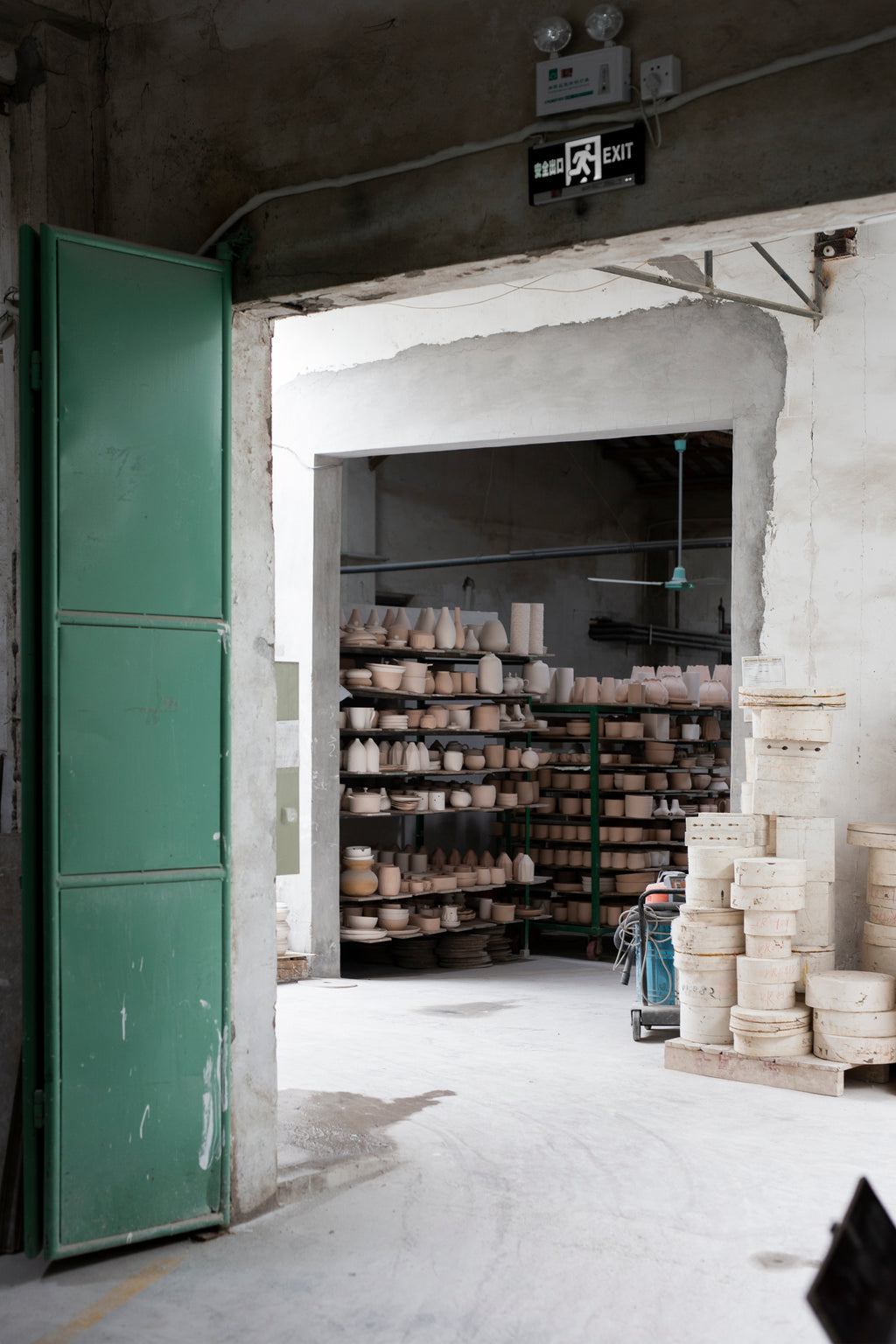
